Mel Sweetnam
unama’ki (cape breton island), canada
Stockholm 101: cold dyeing of purple which is done in the true way
Keep this as a secret matter because the purple has an extremely beautiful luster. Take scum of woad from the dyer, and a sufficient portion of foreign alkanet of about the same weight as the scum – the scum is very light – and triturate it in the mortar. Thus dissolve the alkanet by grinding in the scum and it will give off its essence. Then take the brilliant color prepared by the dyer – if from kermes it is better, or else from krimnos – heat, and put this liquor into half of the scum in the mortar. Then put the wool in and color it unmordanted and you will find it beyond all description.
introduction:
This is a relatively straightforward dye method, though very unusual in that other dyes - in this case, alkanet and either kermes or krimnos (I believe this is safflower) - are blended with woad, rather than a sequential over-dyeing process being used, which is the norm nowadays.
Measures:
There are no measures in this method, other than an indication that the ‘scum of woad’ and ‘foreign alkanet’ should be about the same weight.
Ingredients:
Given the reference to the ‘scum of woad’ being very light, my assumption is that the ‘scum’ is what, nowadays, we refer to as the ‘flower’ - i.e. the mass of bubbles and small particulates that aggregate on the surface of a well reduced indigo vat. For the woad specified in this method, I used woad grown by Ian and Bernadette Howard, in Norfolk, UK. The papyri method does not include instructions for creating the woad vat, so I created a standard reduction vat, but in an attempt to be somewhat authentic, I chose to use a reducing agent that would have been (and still is) very plentiful in Egypt - dates. I used calcium oxide for the alkali. I chose to use cochineal (Dactylopius coccus), since kermes (Porphyrophora spp.) is no longer readily available, and since the active dye compound in each of them is chemically identical - carminic acid.
Process:
I followed the method as faithfully as possible. As it is not really possible to weigh the flower removed from the woad vat without losing some of it in the process, I had to use my eye to gauge how much alkanet to add to the mortar, to try to keep them roughly equal in quantity. In the first instance, I judged relatively equal volumes by eye, but having realized my error, I recreated the method again, this time guessing approximately how much alkanet was required to be equal in weight - rather than volume - to the woad flower. The difference in result between these two approaches is striking. In each instance, I used a mortar and pestle to grind the powdered alkanet into the woad flower. I separately made a cochineal dye bath, from ground cochineal, at approximately 15% the weight of my wool samples, which I held at just below a simmer for an hour. I added enough hot cochineal dye bath to allow the fibres to not be crowded. I mixed the triturated woad/alkanet into the cochineal dye bath, before adding my pre-wetted, unmordanted wool. The method does not say how long to leave the fibres in the combination dye bath, so I chose to leave them in for one hour.


stockholm 93: mordanting for sardian purple
For a mina of wool put in 4 minas of dross of iron (and) 1 choenix of sour pomegranate; but if not this (latter) then (use) 1 chus of vinegar (and) 8 chus of water (heated) over the fire until half of the water has disappeared. Then take the fire away from under it, put the cleaned wool in and leave it there until the water becomes cold. Then take it out, rinse it and it will be mordanted.
introduction:
I uses modern pure chemical ingredients to attempt to replicate the mordant prescribed in this method, in the absence of ready access to some of the original papyri ingredients, such as iron dross. The term ‘Sardian Purple’ in this mordant method is understood to refer to the important dye industry of Sardia, in the west of what is now Turkey. It came under Roman rule in 219 BCE and continued as an important trade centre for many centuries thereafter. My research indicates that some of its important traded commodities included nitrum (soda ash) and coccum (kermes) dyed goods. It was also an important centre of Madder dyeing, which I chose to use to demonstrate the result of this mordant method.
This is the first part (S93) of the series of papyri mordant and dye tests shown in the summary below (Table 1). I chose these particular mordant methods as they represent a range of approaches that may variably affect final dye results. In the case of this method, S93, the presence of ‘dross of iron’ in the mordant implies the intent to modify the final dye colour through iron’s well-known ‘saddening’ of natural dyes, and perhaps, also through the lime treatment, given that hardening water is well known to natural dyers as a technique for achieving richer colour with certain natural dyes.
Measures:
The first challenge was to convert the Greek measures used in the papyri to their modern equivalent. There is no agreed upon modern equivalence for any of these measures, so I took an approximate average from various references/sources.
Ingredients:
This method offers two optional solvents - sour pomegranate or a vinegar/water solution. I opted to use the latter. Some of the ingredients referenced in the papyri are either ambiguous in their meaning and/or not easily accessible to the modern dyer. An example in this particular method is ‘dross of iron’. In mineralogy, ‘dross’ is generally defined as solid materials that float on the surface of a molten metal, such as during smelting, and is usually considered a waste byproduct. In many modern references, the terms ‘tailings’ and ‘dross’ are used interchangeably. Even nowadays, dross is often skimmed off of molten metal for the reclamation of valuable components within it. Iron ore, or any other metal being refined, exists in Nature in combination with a wide variety of other locally occurring metals, and various other inorganic and organic materials. The composition of these additional materials varies widely, depending on the specific geology of the region where the metal is mined. So while the table below is indicative of the wide variety of components that can be found in iron dross/tailings, some at quite high levels, we can not assume that this particular chemical profile is necessarily equivalent to the ‘dross of iron’ to which the papyri author or users had access.
However, as this was the only detailed chemical analysis I was able to find of the composition of iron dross/tailings, I used this study by Adebayo and Onitiri to guide my method, on the assumption that more than just the iron component were important to the papyri author for this particular method. If they weren’t significant, the instructions could have recommended, instead, the use of purer iron filings and vinegar (to create ferrous acetate), as is recommended in several other papyri methods.
In this example, iron (FE2O3) is only 0.0023 (0.23% of total weight) of the total weight of dross. However, experienced natural dyers know that extremely small quantities of iron can significantly shift final dye colour. The three most plentiful components of iron dross/tailings in this analysis are silicon oxide at 61% of the total weight, aluminum oxide at 21%, and calcium oxide (lime) at 12%.
Silicon oxide, the most plentiful component of the dross/tailings analysed in the research referenced above, is an oxide of silicon dioxide, and is ordinarily found in Nature in the form of quartz, and is unlikely to play a chemical role in mordanting.
Aluminum oxide is often created as aluminum in rock seams becomes exposed to air. It is easily soluble in an acid solution, such as the vinegar/water solvent prescribed in this method. Not having access to the aluminum oxide found in dross, I used potassium aluminum sulfate as my aluminum component.
Calcium oxide is quicklime. It is far more reactive (and less safe to work with) than calcium hydroxide (slaked lime), which is just calcium oxide that has been reacted with water. Having easy access to calcium hydroxide, I chose to work with it. While it is poorly soluble in water, which was observed during the mordant preparation, it did provide calcium to the mordant bath, and it is likely that calcium would have been a key component of ‘dross of iron’ in Egypt, given the country’s limestone geology. Many contemporary natural dyers treat fibres with calcium to harden the water in their dye baths, as this can result in more intense dye results with certain natural dyes.
Fe2O3 is ferrous oxide, and is often found in Nature as the mineral hematite. Not having access to hematite, I chose to use purchased ferrous sulfate.
Process:
I followed the method as faithfully as possible, combining the various ingredients as instructed. I heated the mordant bath to a high simmer until the volume had been reduced by half, as instructed. While there is no mention in the method to do so, I stirred every five minutes or so, to ensure that all ingredients were evenly distributed, and to ensure that the the ingredients were as dissolved as possible.
When the volume had reduced by half, I removed it from the heat and added my pre-wetted wool sample, moving the material every so often to ensure even exposure.
I then dyed the sample with Madder (rubia tinctorium), in deference to Sardia’s historic renown for Madder dyeing, resulting in a beautifully rich ruby red with a hint of purple undertones. The woven samples in the images show warp threads using both of the above methods, along with un-dyed organic cotton.


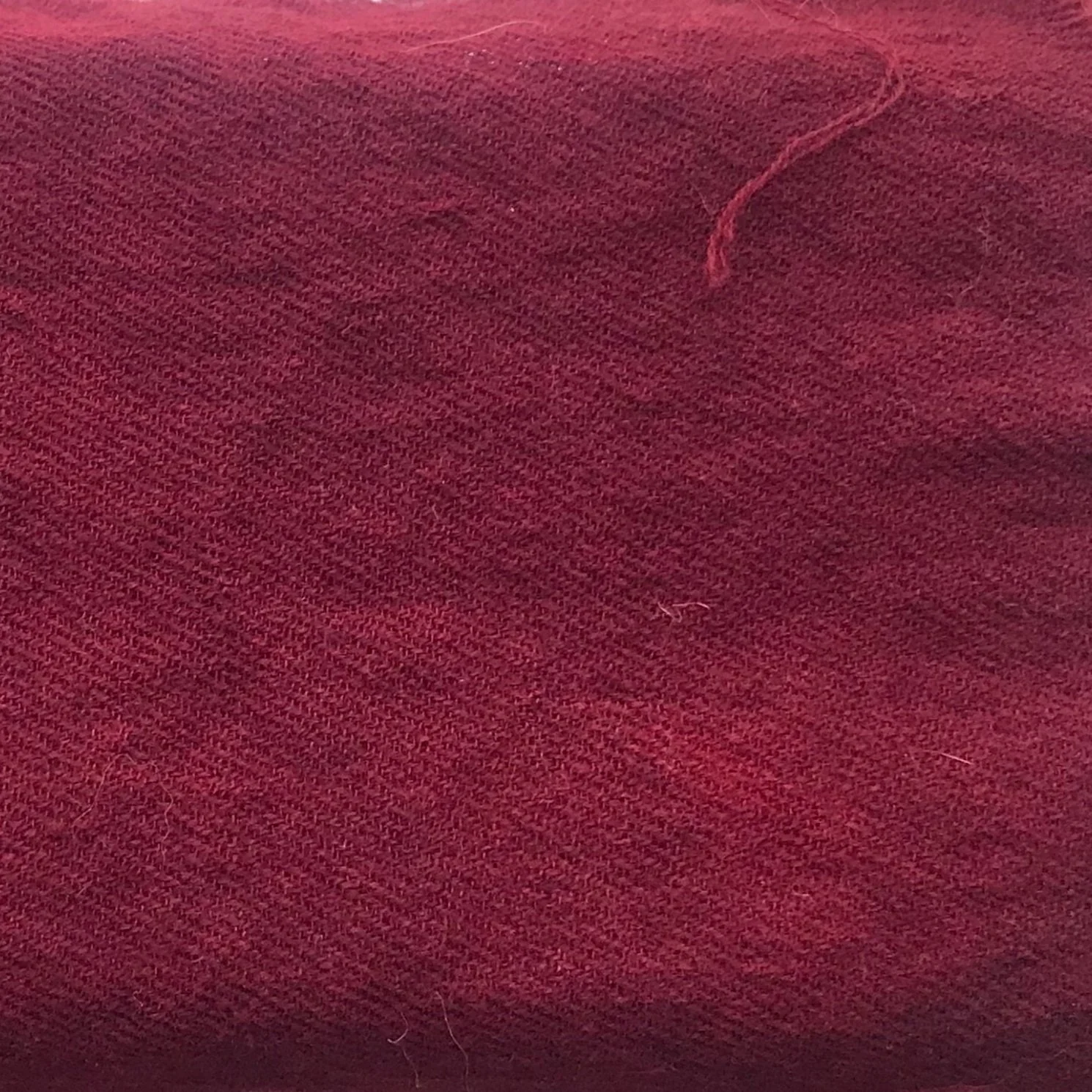